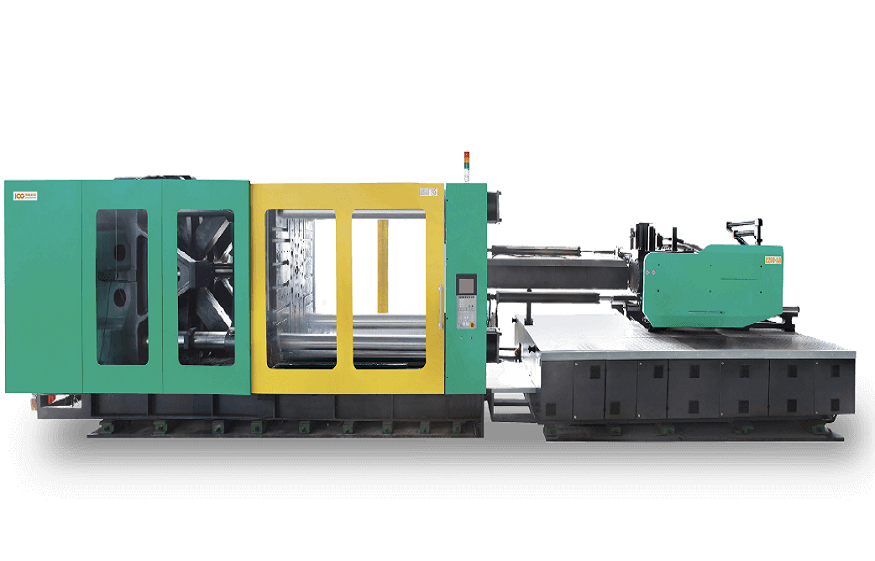
An injection molding machine is essential to the plastic injection molding process. It has different functions. It can produce high-quality products and save costs and time. However, you should know how to choose a plastic injection molding machine before purchasing one. When selecting an injection molding machine, you must consider the following factors.
Alignment system
The alignment system is used to align the mold halves. The alignment system also is used to align the mold halves before they are closed.
injection unit
The injection unit is the heart of the plastic injection molding machine. It provides everything you need to ensure that your project will turn out just right and handle even more pressure than you think it can. Since it’s so important, there are a lot of things that you should know about this part before buying the machine itself.
The first thing to consider when buying an injection unit for your plastic injection molding machine is how much pressure it can handle. This will determine how well your projects look and how much material goes into each one. If too much pressure is put on these machines, they will blow up on us instead of being able to produce what we need them to. Therefore, please ensure that the motor of any model you choose has sufficient power. According to the user mode, the engine will not burn out if it runs for only a few minutes every day/week/month. Pay attention to safety when doing this; Otherwise, accidents may occur. “
Tie-bar
The tie-bar is the part of the molding machine that holds the mold halves together. It may be made of steel, aluminum, or stainless steel with a smooth surface. Usually, tie bars are straight and either round or square in cross-section.
Tie bars hold the mold halves together while the concrete is poured. They also provide strength and support for the mold while it is in use. Tie bars can be made of steel, aluminum, or stainless steel with a smooth surface.
Die locking
Die locking is fixing the molding tool to the tooling plate. It is done with a die lock ring or a different die lock frame. Different types of dies can be used in injection molding machines, and it is essential to ensure that these parts do not move relative to each other during the injection. This provides efficient production, reduces waste, and improves quality control over your product.
Nozzle and sprue bushing
The nozzle is a critical piece of the injection molding machine. It injects molten plastic into the mold, which must withstand high pressure and temperature. At the same time, it can be cooled quickly so that the next injection can be carried out in time.
The nozzle is made of hardened steel or cemented carbide, but that doesn’t mean you should go out and buy nozzles made of these materials. Unless you are sure, they are suitable for your situation (if you are, we’d love to hear about them!). The main thing is that your nozzle has an opening at both ends for cooling liquid (one for pouring and one for draining), which allows heat transfer away from the molten plastic.
The length usually expresses the size of the nozzle as the diameter. She meant that it might only be necessary to drill a 5mm hole in the metal pipe with a threaded end. So she can screw them onto existing equipment without making anything herself.
Heater bands and temperature controllers
The heating of the mold is an essential part of the plastic injection molding process, as it helps prevent warping and cracking while keeping the plastic in its liquid state. Heater bands are used to heat the plastic so that it can be injected into molds quickly. When selecting a heater band, you need to ensure that it has enough power and control over temperature levels compared with other models on the market.
Temperature controllers are also significant in this process because they help maintain a specific temperature within your mold during use. This way, you know exactly how much heat will be transferred through each part of your injection-molded product!
Barrel cooling
The barrel cooling system is essential for the plastic injection molding machine. It must be able to cool the barrel with water or air. The number of cooling points and channels must be sufficient to meet the required cooling capacity so that each channel can provide enough pressure and temperature to ensure that the product can be effectively cooled.
Hot runner system (optional)
Hot runner systems feed plastic material into the mold and control the temperature of the plastic material. They are optional but help to reduce cycle times, improve quality and reduce scrap.
Must read these points before investing in the plastic injection molding machine
Before investing in the plastic injection molding machine, you must know what you will buy and how this machine can be used. You must have a clear picture of all the features of the plastic injection molding machine because only then will you be able to make an informed choice.
Let us start with understanding what a plastic injection molding machine is. “molding” refers to forming something from another substance. In contrast, “plastic” refers to any synthetic product synthesized or processed from crude oil. Hence, a plastic injection molding machine is used for making different products using plastics by injecting molten plastic into molds preheated by an external source. This process allows manufacturers to produce parts with complex geometries and shapes. Compared with other methods (such as machining or casting metal into steel blocks), production cost or time consumption is not too difficult!
In the end
It is important to note that you can’t just choose any plastic injection molding machine and expect it to work for you. These machines are expensive and require a lot of maintenance before purchase. Make sure you know what device will work best for your business needs.