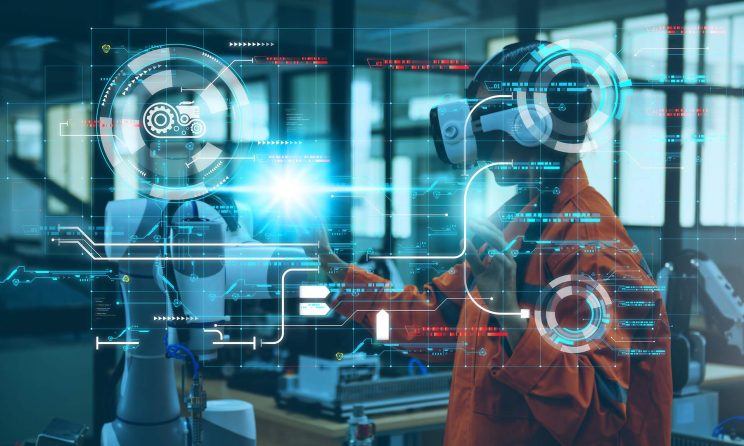
In the realm of manufacturing and construction, welding stands as a cornerstone process, fusing metals together to create structures that are both functional and intricate. Traditionally, this art has relied heavily on the skilled hands of human welders, employing techniques like TIG (Tungsten Inert Gas) welding. However, with the rapid advancement of technology, a new era has dawned upon welding – the era of robotic TIG technology.
Welding, in its simplest form, dates back to ancient times, where blacksmiths forged metals together using heat. Over centuries, this craft evolved, culminating in the techniques we know today. TIG welding, in particular, emerged as a precise method, utilizing a tungsten electrode to generate the arc and inert gas to shield the weld area from contamination. Yet, despite its efficacy, traditional TIG welding faced limitations in speed, consistency, and accessibility.
Understanding Robotic TIG Welding
Robotic TIG welding heralds a new era, blending the precision of TIG welding with the efficiency of automation. These systems consist of robotic arms equipped with welding torches capable of executing intricate welds with unparalleled accuracy. By harnessing robotics, manufacturers can achieve consistency in weld quality across large-scale production runs, reducing defects and rework. Moreover, robotic TIG welding finds applications across diverse industries, from automotive manufacturing to aerospace engineering, showcasing its versatility and adaptability.
Robotic TIG welding systems are equipped with advanced sensors and vision systems, allowing them to analyze weld parameters in real time. This capability enables robots to make adjustments on the fly, ensuring optimal weld quality and performance. Additionally, automation minimizes the risk of human error, leading to higher productivity and throughput. As a result, manufacturers can meet stringent quality standards while increasing efficiency and reducing costs.
Technological Advancements in Robotic TIG Welding
Advancements in robotic TIG welding have propelled the technology to new heights. Automation, coupled with artificial intelligence, enables robots to analyze weld parameters in real time, adjusting settings for optimal performance. Enhanced precision, achieved through advanced sensors and vision systems, ensures welds meet stringent quality standards. Furthermore, ongoing research has expanded the repertoire of materials compatible with robotic TIG welding, opening doors to innovative design possibilities and improved performance.
One of the most significant advancements in robotic TIG welding is the integration of collaborative robotics. These systems allow humans and robots to work together in close proximity, leveraging the strengths of both. Human operators can oversee complex tasks and provide guidance, while robots handle repetitive or hazardous aspects of welding. This collaborative approach enhances productivity and safety while fostering a more dynamic and flexible manufacturing environment.
Impacts on the Welding Industry
The rise of robotic TIG welding signals a paradigm shift in the welding industry. While traditionalists may lament the potential displacement of skilled welders, the reality is a more nuanced blend of human expertise and technological advancement. Robotic TIG welding streamlines production processes, reducing labor costs and cycle times. However, it also necessitates a shift in workforce dynamics, requiring workers to adapt and embrace new skills, such as programming and robotics maintenance. Despite these challenges, the economic and environmental benefits of robotic TIG welding cannot be understated, driving its widespread adoption across global markets.
In addition to its impact on the workforce, robotic TIG welding also has far-reaching implications for product design and innovation. With the ability to weld complex geometries and a wide range of materials, manufacturers are empowered to push the boundaries of what’s possible. This opens up new opportunities for lightweight, structural optimization, and performance enhancement across a variety of industries. Furthermore, the consistency and repeatability of robotic TIG welding enable manufacturers to produce higher-quality products with greater efficiency, enhancing their competitiveness in the global marketplace.
Challenges and Considerations
As with any technological advancement, robotic TIG welding poses its share of challenges and considerations. Technical hurdles, such as programming complexities and equipment maintenance, must be addressed to ensure seamless integration into existing workflows. Safety remains paramount, with stringent regulations governing robotic operations to mitigate risks to human operators. Moreover, the ethical implications of automation in the workforce warrant careful examination, balancing efficiency gains with concerns over job displacement and worker well-being.
Future Prospects and Opportunities
Looking ahead, the future of robotic TIG welding brims with promise. Continued innovation promises to enhance productivity, reliability, and versatility further. Integration with Industry 4.0 initiatives and the Internet of Things (IoT) heralds a new era of interconnected manufacturing, where robotic systems communicate seamlessly with other production assets. Collaborative robotics, where humans and robots work side by side, offers opportunities for synergy and efficiency. As industries evolve and demand shifts, robotic TIG welding stands poised to lead the charge into a new era of manufacturing excellence.
Conclusion
In conclusion, the advent of robotic TIG welding represents a watershed moment in the evolution of welding technology. By marrying precision with automation, these systems redefine the boundaries of what’s possible, driving efficiency, quality, and innovation. While challenges abound, the potential for transformative impact is undeniable. As industries embrace the future of welding, embracing technological advancements with open arms, the stage is set for a new era of manufacturing excellence, where human ingenuity and robotic precision converge to shape the world of tomorrow.