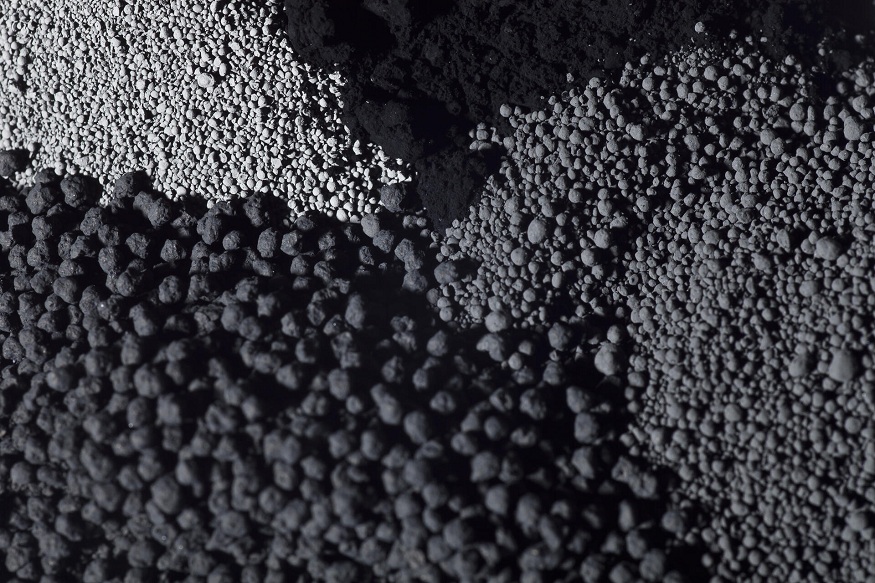
Not all of the carbon black are created equal and there are significant differences in multiple options of carbon black available in the industry. Normally organisations only consider the cost of carbon Black as a point of differentiation but there are several other points that you need to take into account specifically from the perspective of the compounding process. There are a good number of factors including the letdown ratio, drop-in ratio and other factors that you need to consider so that you will be very much aware of the basic properties of the particular cabin and black that you are using. Following are the common mistakes that you need to avoid at the time of mixing carbon Black for plastics application and the useful tips associated with compounding that you need to know are justified:
- Choosing the wrong carbon black for the job: Since every type of carbon Black has been designed with the motive of dealing with a significant range of applications, the carbon black that you will be choosing will have a particle size, aggregate size and surface chemistry that might not be suitable as per your process and application. For example, if the carbon black that comes with a very high structure will be suitable for conductive applications, one with a very high surface area will be better suitable for applications that require very high elements of tinting. So, in this particular case, you need to be very clear about proceeding with the choice of the correct carbon black for your project so that everything has been designed for your application without any issues at any point in time. This will be helpful in making sure that everything will be very well sorted out right from the beginning without any problem at any point in time.
- Usage of the incorrect letdown ratio: If the LDR of the master batch is very high or very low as per the intended application, you will end up with a very wrong mixture due to the large viscosity mismatch. So, by the same token, you definitely need to have a clear idea about the usage of the right current Block in the injection moulding process so that calculating the correct LDR will be very well done. If the things are not at all paid attention to, it will lead to very poor quality in your finished components and further you need to be very much aware of the basic calculations. So to achieve accuracy in the cases of Birla carbon products, you definitely need to get in touch with the right processes that come with very correct calculation of LDR so that there is no scope of any kind of problem and the things are perfectly sorted out.
- Usage of the aggressive compounding process: Ideally the compounding process should always focus on separating your carbon black agglomerate into aggregates which will disperse evenly along the base polymer and help in the creation of a very smooth overall compound without any breakage into the structure. But there are a good number of engineers that are compounding things into machinery with the wrong geometry due to which the compounding process is prone to a significant number of mistakes and becomes much more aggressive or electrically conducive plastic like carbon black. So, the overly aggressive compounding process in this particular case will compromise your performance of the carbon black by breaking down the structure which is the main reason that you need to be very sure about optimising the compounding line upfront without any problem right from the beginning.
- Going for improper handling and storage of the samples: Even before you have created the optimal carbon black compound, improper handling and storage scenarios will lead to a significant number of issues for your hard work. There is a significant number of samples that are usually stored in human conditions that lead to excessive pick up of moisture or the storage has been done into dust prone environment which gives these significant number of issues in the whole process. So that the rhyme of having a clear idea about the compounding related to carbon black in tyres, you definitely need to be clear about the appropriate handling and storage so that there is no scope of any kind of problem. Factors like these will negatively impact the compounding process and eventually will decrease the performance of the final product. So, keeping a closed eye on your storage requirements will be very important throughout the process so that there is no scope for any kind of practical difficulty with the carbon black at any point of time throughout the process.
- Using the familiar drop-in instead of the custom process: Once you have a good command over the drop-in process that works for a particular type of carbon black, you definitely need to assume that everything will be safe in terms of using and further the same category of drop-in has been used for other types as well. But this will be a big mistake. Every drop-in process will require you to become much customer of a specific carbon black product so that users and other associated things will be very well sorted out and you need to achieve the element of optimum performance without any problem. Additionally having a clear idea about the custom process will be very important so that there is no scope for any kind of issues and things are very well sorted out.
- Failure to control the impurities: Even seemingly minor impurities will negatively impact the performance of the carbon Black which is the main reason that having a clear idea about the dispersion and smoothness of the surface will be very important so that is no scope of any kind of rejection and everyone will be able to enjoy next level of cleanliness without any issues at any point of time
Hence by avoiding all of the above-mentioned mistakes you will be able to achieve the best possible results you have been aiming for and further the final product will be performing according to the specifications without any problem. With a little attention to the details, you will be able to create the best of the carbon black compounds that will be exactly turning out the way you actually wanted.